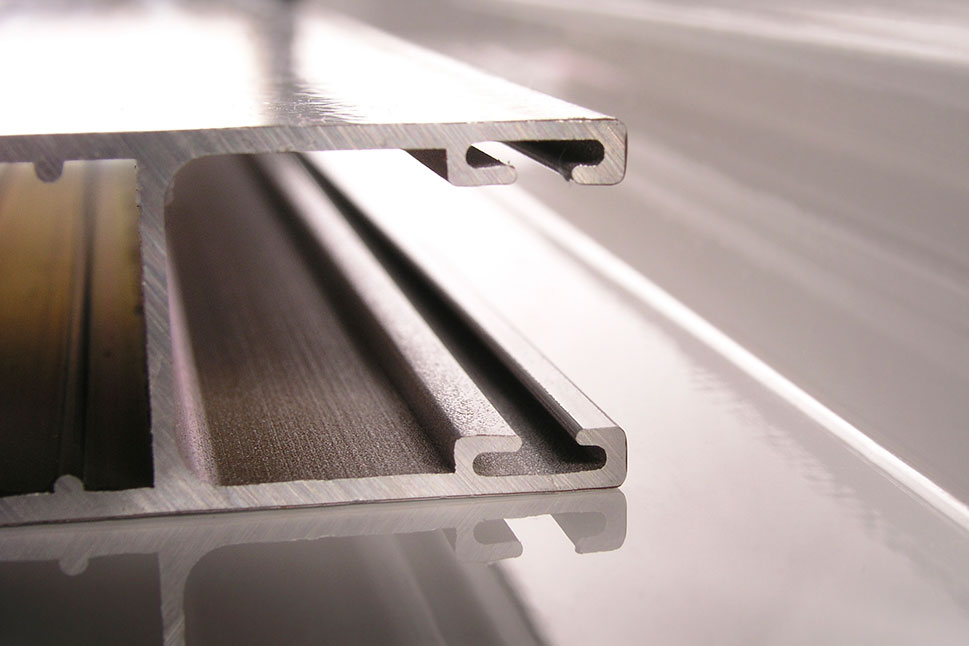
To Optimize Nitrogen Shrouding, Factors to Consider Include:
- Most cost-effective supply mode: gaseous, liquid, or on-site generation
- Where to introduce nitrogen: die backer, bolster, platen/canister
- How to establish optimal nitrogen flow rates
- Tooling grooving patterns and consistent connections to tooling
- Equipment issues, like undersized hoses/fittings, minimal flow controls and flow measurement
- Nitrogen leakage
- Poor nitrogen distribution on multi-hole dies
- How many shapes and alloys extruded
- Solid, hollow, or multi-hole dies
- Single or double die slides
- Tooling purchased from other extruders with different grooving, connections, etc.
- Insufficient nitrogen flows to provide proper cooling and inerting
Helping Aluminum Producers Optimize Production and Economics
Light Metal Age’s Ann Marie Fellom sat down with Air Products’ Russell Hewertson at the ALUMINIUM USA trade show in Detroit, Michigan, as part of the magazine’s interview series with notable members of the aluminum industry. In his interview, the Americas Commercial Technology Manager at Air Products discussed the importance of close collaboration with aluminum producers to help them optimize their operation through our expertise, gases and technologies.
Check out our brief video excerpts from the full interview that answer some frequently asked questions.
Count on Air Products' expertise...
Our applications engineers can help you optimize nitrogen performance in your extrusion process.
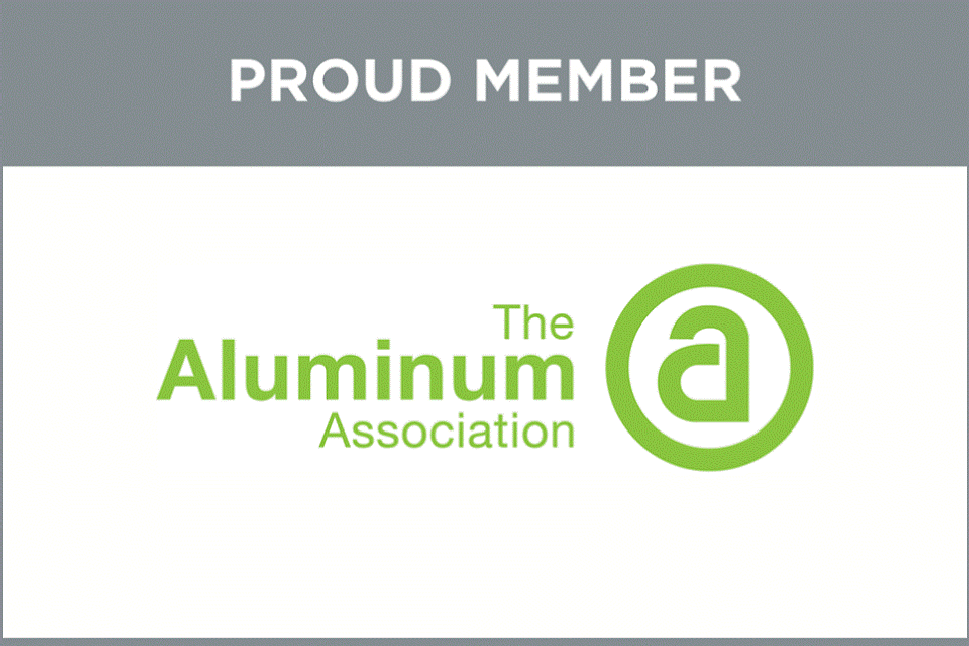
Advocacy. Standards. Insight.
The Aluminum Association is the industry’s leading voice in Washington, DC. It provides global standards, industry statistics and expert knowledge to member companies and policy makers nationwide. Highly engaged in public policy and technical forums, the Association is committed to advancing aluminum as the sustainable metal of choice around the world.